What to Know About Building a Pole Barn in Minnesota
Poles in the ground anchoring a structure. A simple construction concept that originated in the 1930s has grown to become a go-to building approach for its economic and multi-purpose advantages.
When you embark on your first pole barn construction, you'll quickly realize it’s a project that goes beyond installing four poles and a slab. However, with the right engineering and design, the effort and investment are more than worth it in the end. Pole barns are not just environmentally friendly and affordable; they offer durability and energy efficiency and maintain their value over time.
If you’re thinking about building a pole barn in Minnesota, we’re here to explain the key things to know, like:
- Basic steps in the pole barn building process
- Land clearing and foundation requirements
- The most important aspects of pole barn design
- Tips for selecting materials and a builder
First, Learn the Builder Terms We Use in This Post
Continuous foundation: In stick-built construction, the framing system is typically built on a completely flat, continuous concrete slab that secures the walls to the floor.
Girt: A funny word that essentially means structural beams, which provide lateral or vertical support to a post-frame building.
Post-frame construction: Buildings with large columns – highly engineered, prefabricated posts – instead of wood studs, steel framing, or concrete masonry.
Stick-built construction: Commonly used for houses, buildings with a wooden skeleton constructed on-site, stick by stick. (As opposed to prefabricated in a factory.)
And to Clarify, a Pole Barn Is…?
It’s a term used to describe buildings framed by wooden posts with high ceilings and no basements. You may have also heard them called “pole buildings” or “post-frame.”
…or “shouses” or “barndominiums,” if you’re feeling clever!
Originally designed for agriculture back in the day, pole barns have undergone a transformation with every decade since and are now used for a wide range of purposes.
From greenhouses and garages to workshops, dance studios, storefronts, event centers, horse stables, and even modern housing – the possibilities are endless.
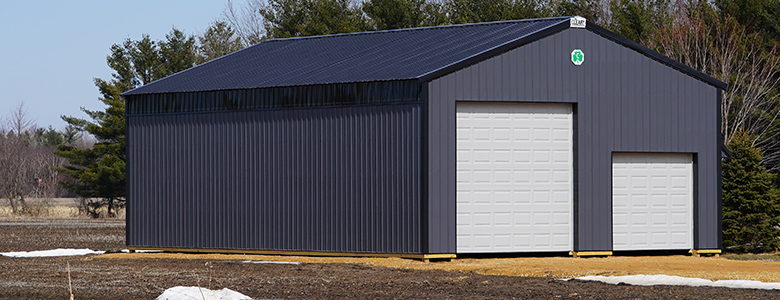
The Basic Steps to Build a Pole Barn
Pole barn construction involves clearing land, creating a foundation, and burying prefabricated laminated wooden posts to provide a supportive frame.
As the main vertical framing element, the posts, also known as columns, are reinforced with concrete and typically connected with wood sidewall girts.
A concrete slab is often added, though it is not necessary to have a full slab or even any floor at all to make the structure sound. A builder can sink the columns directly into the ground since the walls and floor work independently from one another, allowing a pole barn to hold more weight and remain stable.
Without the need for a continuous foundation, building a pole barn is a much simpler, cheaper construction process than stick-built construction.
In Minnesota, What Are Pole Barn Land Requirements?
Obviously, you have some land if you’re thinking about building a pole barn. Depending on its condition, the land will need to be cleared.
If it’s a heavily wooded area, that could be a significant job; if it’s an open, relatively flat patch of dirt, clearing and building can happen much sooner. It’s not unheard of for a pole barn to go up in a single day!
For that to happen in Minnesota, there’s paperwork. You must know and comply with your zoning laws, building codes, and neighborhood covenants, especially if you want to build a pole barn for housing.
When the intended use is a dwelling, building permits are required for inspections and to verify code compliance with Minnesota laws.
The Design Elements That Make or Break a Pole Barn Design
When the internet helped people re-realize the benefits of pole barns and post-frame construction, these builds took off in a new way. And with a boom in pole barn building came a wide spectrum in the quality of these construction projects.
DIY pole barn building is widely searched on Google, and even some “professional” builders are winging it with limited knowledge and experience. You can buy a pole barn kit online. The simplicity of the structure means that some people underestimate all that goes into a successful construction project.
An expert design-builder doesn’t underestimate any project. An expert will plan thoroughly. An expert will design your pole barn thoughtfully for access, capacity, and traffic patterns, and they will carefully comply with the standards for post-frame buildings outlined by NFBA, the National Frame Building Association.
For example, the NFBA recommends three types of pole barn foundations:
- Treated wood embedded directly into the ground
- Asphalt and plastic protection sleeves
- U- or L-shaped construction brackets and non-treated wood bolted into concrete
Whether you are forging ahead with DIY construction anyway or simply want more insight into what a professional considers, let’s take a brief look at the design elements that can make or break your pole barn’s durability, functionality, and aesthetics.
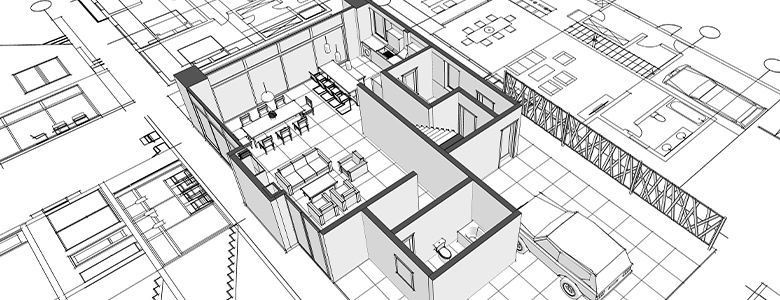
Dimensions
Go big or go home, right? Pole barns are a cheap build, so you might as well design yours to be massive!
…unless you want it to work for its intended use.
Dimensions of your pole barn should be carefully calculated based on actual use, with doors and interiors always top-of-mind.
Engineering
Here’s what the average person is going to lack: the engineering knowledge needed for designing the columns, trusses, and other components.
An in-depth understanding of post-frame load requirements. Condensation control systems for metal roofing. Soundproofing materials. HVAC, plumbing, and electrical requirements.
…and so many other aspects of engineering that are not common knowledge and too complex for a YouTube video masterclass.
Insulation
It’s not really an option in the Land of 10,000 “Last Snowstorm of the Season”s. And it’s the law if you want to live in it.
You need insulation in your pole barn – the amount will be based on what you use it for.
Ventilation
Rookie mistake: not designing your pole barn for adequate ventilation.
Good indoor air quality is paramount, whether your pole barn will be used by humans or animals or for storing equipment and/or chemicals.
Choosing the Right Pole Barn Materials & Builder
If you’ve made it this far and still want to build a pole barn from the ground up by yourself, hopefully, this isn’t your first construction rodeo. You must be an experienced builder to complete this project at a high level and perfect all the design elements.
If that’s the case, then you already know building material selection is key, so feel free to drop out here and get to planning!
…if you’ve realized you’ve bitten off more than you can chew, may we suggest getting an estimate from a pro? It doesn’t mean you can’t handle this build, it means you know what you want and understand the easiest, fastest way to make it happen.
From materials selection to obtaining permits to construction to cleanup, hiring a professional to build a pole barn is the smart choice.
But speaking of pole barn material selection, as promised, here are a few tips:
- “Saving money” by using low-quality materials will only lead to higher maintenance, replacement, and energy costs in the long run. You’re already saving money by building post-frame; invest in premium brands for durability against Minnesota’s tough weather conditions.
- A key determiner to the overall cost-effectiveness of your pole barn and its cost? Choosing the right doors and windows! In part because pole barns have such big roofs, where water drains off and can splash back, the long and short-term viability of your building depends on water-resistant, well-made, professionally installed windows and doors.
- If you don’t want or need to insulate the entire building, you will likely still need to figure out insulation for the metal roof. A non-insulated metal roof will cause too much condensation.
Olson Construction & Remodeling Builds Pole Barns in Minnesota
We hope you got some answers to your questions about building a pole barn in Minnesota. With decades in this industry, our owner has a few insights up his sleeve!
We also hope we convinced you to consider hiring a professional for your project, like our guy Nick Olson – an Architectural Draftsman with the ability to personalize your pole barn design and create blueprints in-house from start to finish.
He might even bring his dogs to the job site if they feel like working that day!
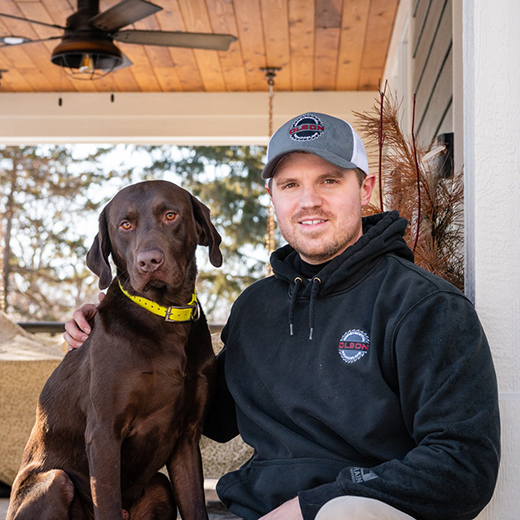
If you’re interested in getting an estimate for your project, contact Olson Construction & Remodeling . We’re based in Oakdale and Stillwater, Minnesota, and we absolutely LOVE to design and build custom post-frame buildings throughout the greater Twin Cities area.
We also serve some areas of Wisconsin near the east metro, and our customers have great things to say about us .
Here’s a little sample of our work . Give us a call at 651-279-2590 or fill out one of our online forms to reach out today!